Assignment: To create a wooden toy with a critical focus on durability, finish, and, execution.
Description: A single piece wooden truck with an acrylic, spring powered pull-back motor and rubber tires.
I aimed to create a simple, yet recognizable design that was animated enough to appeal to younger children, but stylized enough to still be a beautiful form.
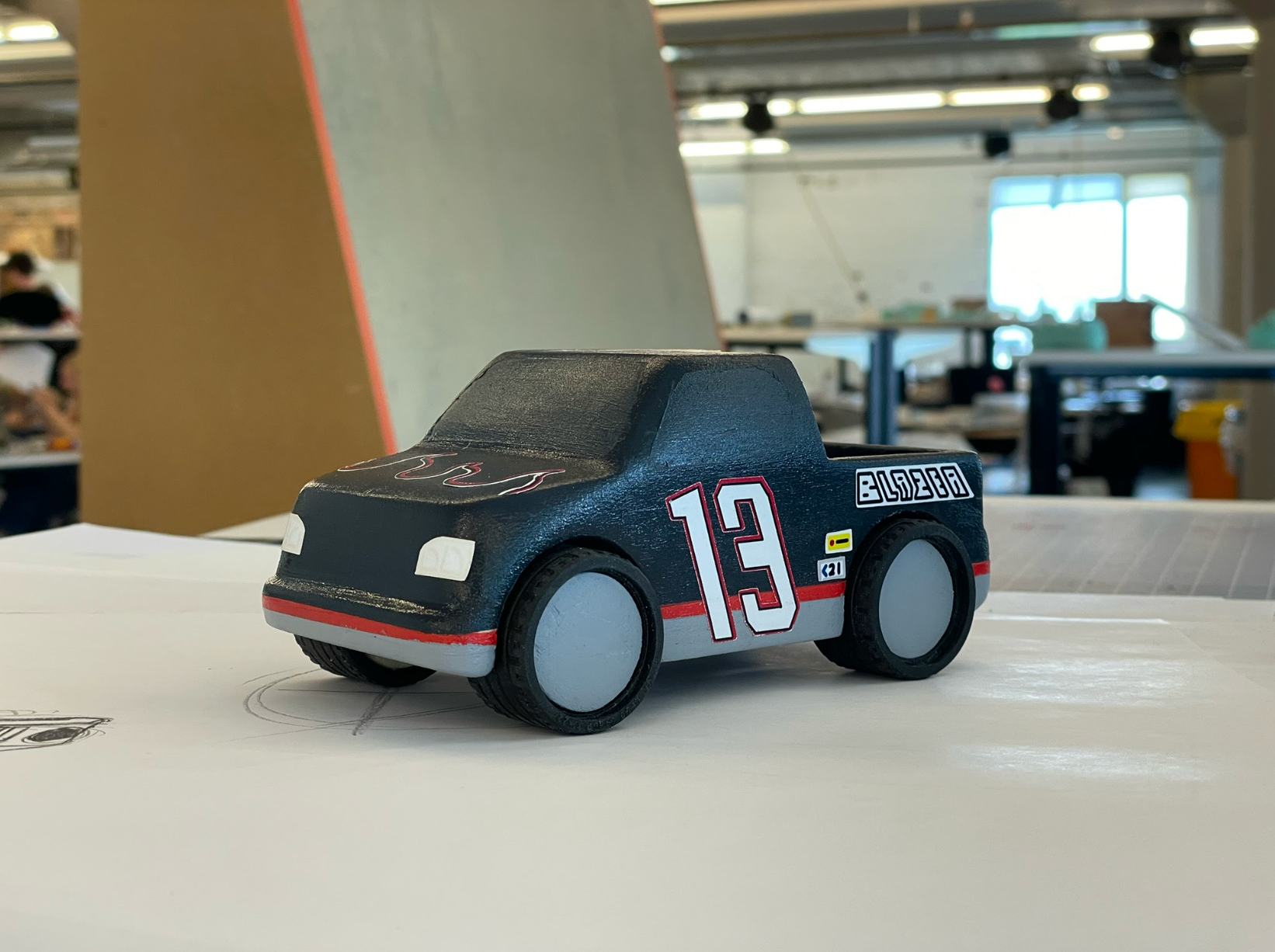
Initial Concept Generation
I began this design process with three different concepts, but after in-class critique I selected my car idea. I had two primary functions I was deciding between: swappable wheels or a pull back motor. Though the swappable wheels would have been easier, I elected to go for the pull-back motor instead as it makes the toy more dynamic.
I sketched through a variety of different forms, taking inspiration from a wide range of cars. I also explored levels of realism and simplicity.
I decided to go with a simplified, rounded sports car design.
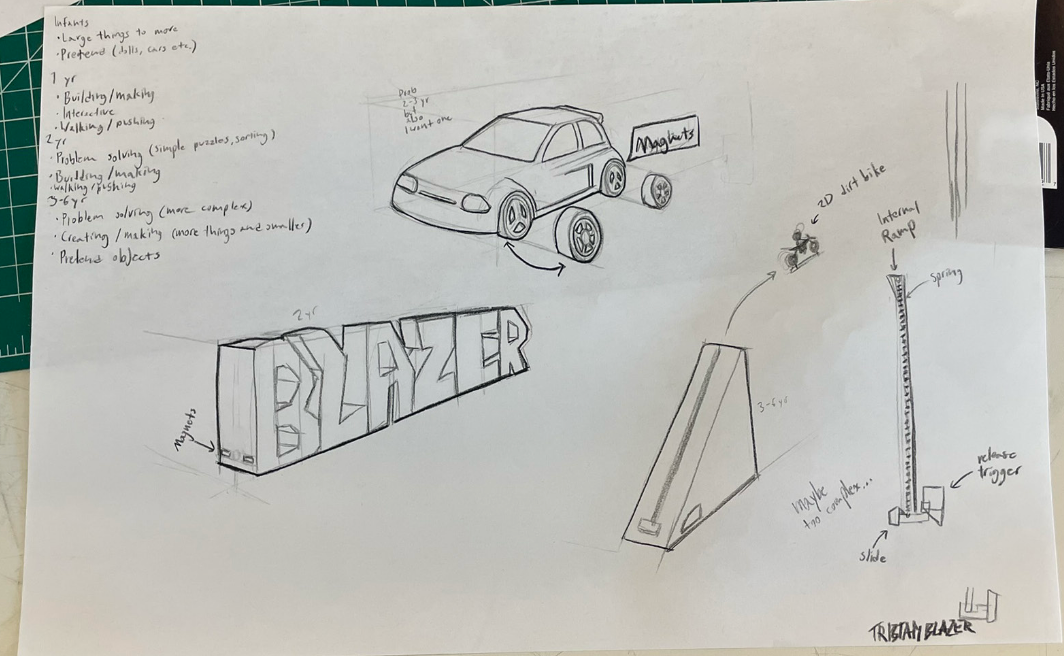
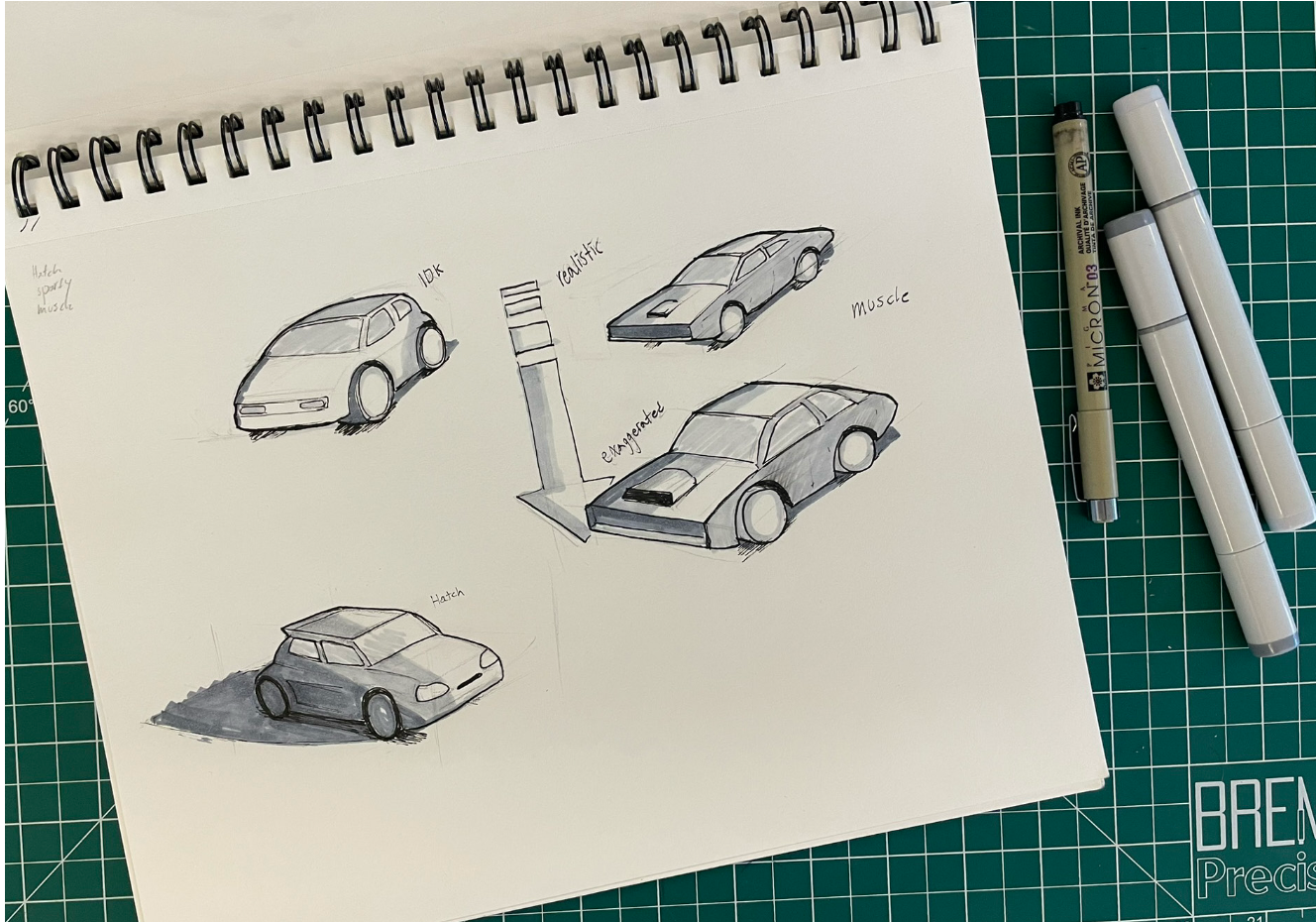
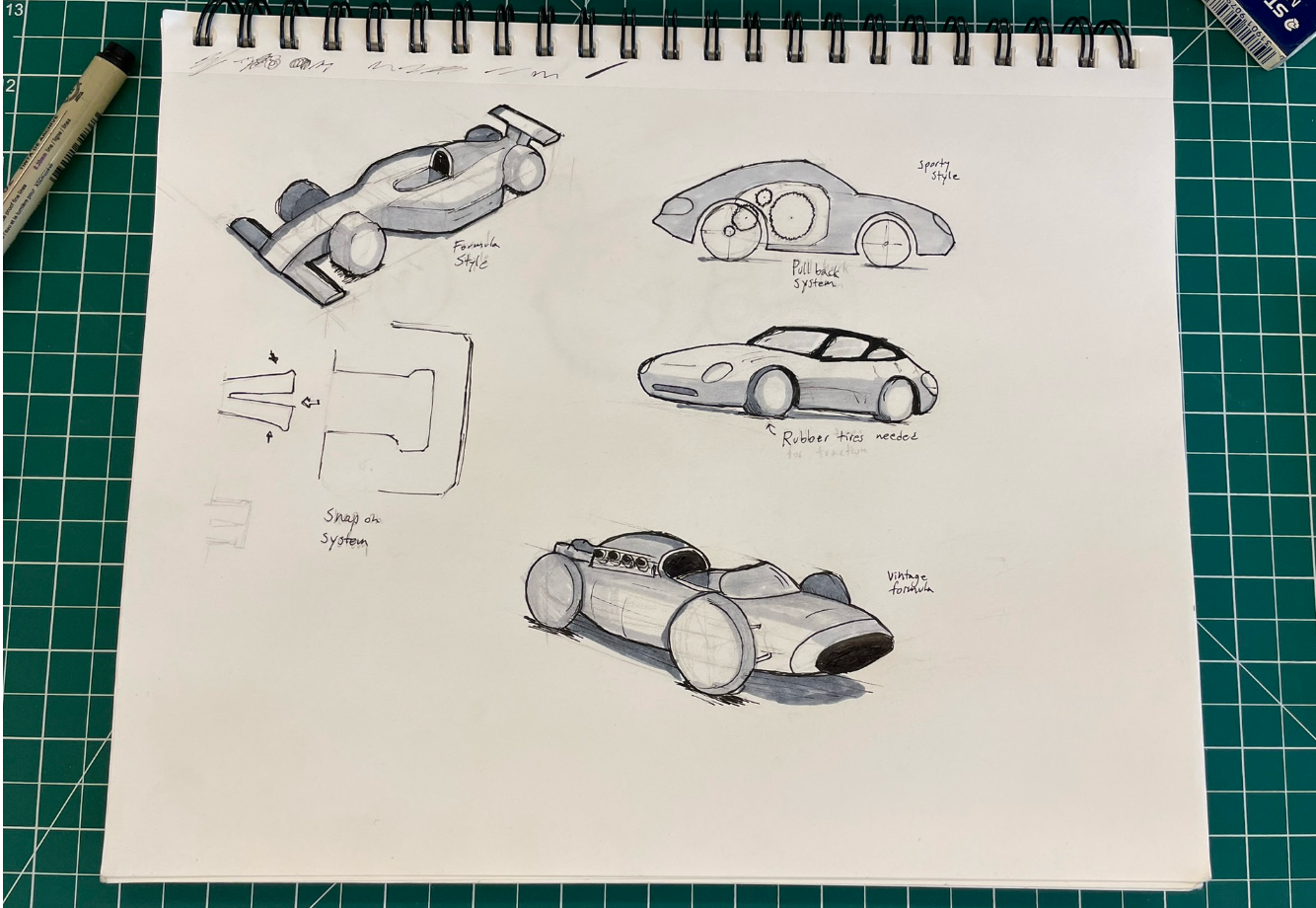
Plasticine Model
To work out sizing and general proportion I made a mockup out of plasticine clay.
Mechanism Research
To research how to build my own pull-back mechanism I disassembled a toy car. I then modeled my custom gearbox in CAD software based on the dimensions worked out from the plasticine mockup.
Idea Revision
I ran into an issue with dimensions while searching for a suitable spiral torsion spring. I was only able to find one for sale that would somewhat work with my sizing. However, it required me to make all my gears larger as it was slightly oversized. This meant that the largest gear in my gearbox would have less than an eighth inch of clearance from the windshield.
Rather than making the car bigger, I designed a new simplified pickup truck form that would look natural with a more vertical windshield. This form also allowed me to display the pull-back mechanism in the bed, rather than hide it.
MDF Gearbox
My initial plan for the gearbox was to construct it out of MDF with metal axles. I laser cut the pieces and assembled it with superglue. I went through three revisions of the MDF gearbox alone, as the gears would get stuck when unwinding, and the main gear attached to the spring could tilt and jam. To fix these issues I increased backlash on all gears and added a brace for the main gear to hold it in place.
Despite successfully fixing these issues, I still was running into problems where gears would skip after a few rounds of use. This occurred from the natural softness of MDF, which caused the thin, pointed teeth to mash down until they no longer meshed correctly.
Acrylic Gearbox
I switched to acrylic for my gearbox as it is easy to cut on a laser cutter, and significantly more stiff than MDF. I considered 3D printing the gears though decided against it as they would likely be weak at such a small size. I researched similar products and nylon seems to be the typical material used. However, I did not have the resources to manufacture it.
The acrylic worked significantly better than the MDF. It meshed more consistently, shifted less, and looked more visually interesting.
Gearbox slot
I began work on the wood by milling out the slot for the gearbox to sit in. I measured depths at sixteenth of an inch intervals and created a stepped slope using the mill. I also made a test piece of wood that represented the gearbox with added clearance which I used to measure my slot. I sanded the inside to make a smooth curve and tested repeatedly until it fit.
Rough Shape
I drew a dimension accurate sketch on the wood and used it to cut wheel wells and a very rough shape of the truck.
Bed
To make the bed I used a similar technique as I did with the gearbox slot. I created a stepped cut using the mill, then finished shaping with a chisel and sandpaper.
Body finishing
I sanded the body with coarse sandpaper until it was a shape I was happy with, then finished sanding until smooth.
For tires I used LEGO tires and cut wood cylinders to fit inside them. The rubber tires were necessary for the pull-back motor as wood wheels would not get adequate traction.
Painting
I developed multiple design styles and combined elements of my favorites.
I created a sticker sheet which I printed and cut using a classmate's Cricut. I then painted the truck, applied the stickers, added some layers of clear coat and assembled the final product.
Conclusion
Overall I am really happy with how this project came out, though the process was far from smooth. Just the making of the truck body itself was a very labor intensive process.
The real challenge, however, was the gearbox. In the end, the acrylic gears shared a similar short lifespan as their MDF predecessor. The brittle nature of acrylic caused the teeth to shatter upon high impact, which happened regularly when releasing the truck. Ultimately nylon or aluminum would have solved these issues however a lack of resources prevented me from using them.
The truck alongside various other classmate's toys.